Technology in the service of health
Studies on professional musicians confirm again and again that they suffer particularly often from diseases of the musculoskeletal system. The spine, neck, shoulder area and wrists of the blower are at risk of wear and tear. Horn player arms even carry twice the weight: on the double horn, on the triple horn!
Light valves
At FINKE, the "light horn" became development goal No. 1. A starting point was provided by the brass valves that Stölzel had brought to maturity in 1815. It was not until 150 years later that instrument makers attempted to replace the heavy metal with lighter materials. Initial developments were difficult, as the new "sleeve valves" were too often stuck: Thermal expansion was the problem.


While most manufacturers have lost their interest in plastic valves, FINKE brought the Bielefeld University of Applied Sciences into the company. A time of thorough research, some self-doubts and large investments finally brought them to life: the everyday suitable valves made of all-plastic with stainless steel axis. They could either only be made to measure or not at all. That is why they are also interchangeable with one another.
But the skepticism of many musicians remained. They remembered the setbacks of the pioneering days and they still suspected cheap plastic material where in reality high-performance materials are used. These polymers can easily compete with the best metal alloys because they are incredibly wear-resistant and resilient. The FINKE horns have long since earned the trust they and their plastic valves deserve. Distributed in hundreds of copies all over the world, they can be blown under all climatic conditions without any problems.


At a glance
- Plastic valves do not oxidize, which is why conventional valves wear out.
- Maintenance is limited to cleaning - the blower can do that himself.
- The slight inertia of the mass becomes noticeable at the touch of a button - relief for the wrist.
Slim tubes
FINKE did not only make the valves "slim". Thin-walled bends and tubes brought a weight reduction of 30%. Solidity and response remained unaffected, not even slightly deteriorated. Finally, the small parts were slimmed down. Among other things, this resulted in a valve cover made of polished aluminum. The usual brass cover weighs at least three times as much. The result: FINKE horns are among the lightest on the market!
The sound makes the music
The acoustics of the instruments were worked on with the same thoroughness. The horns that have become lighter should also be easier to blow. FINKE was one of the first manufacturers to seek advice from Braunschweig. In years of collaboration with Dr. Klaus Wogram from the Acoustical Institute of the Physikalisch-Technische Bundesanstalt managed to improve the mood and response of the FINKE horn well above the average! This is especially true for the high location. Light in weight, easy to respond, clean in tone: This is how FINKE horns became sound horns. FINKE will continue to strive to make good things even better in the future. More and more wind players are discovering that they have a clear advantage!
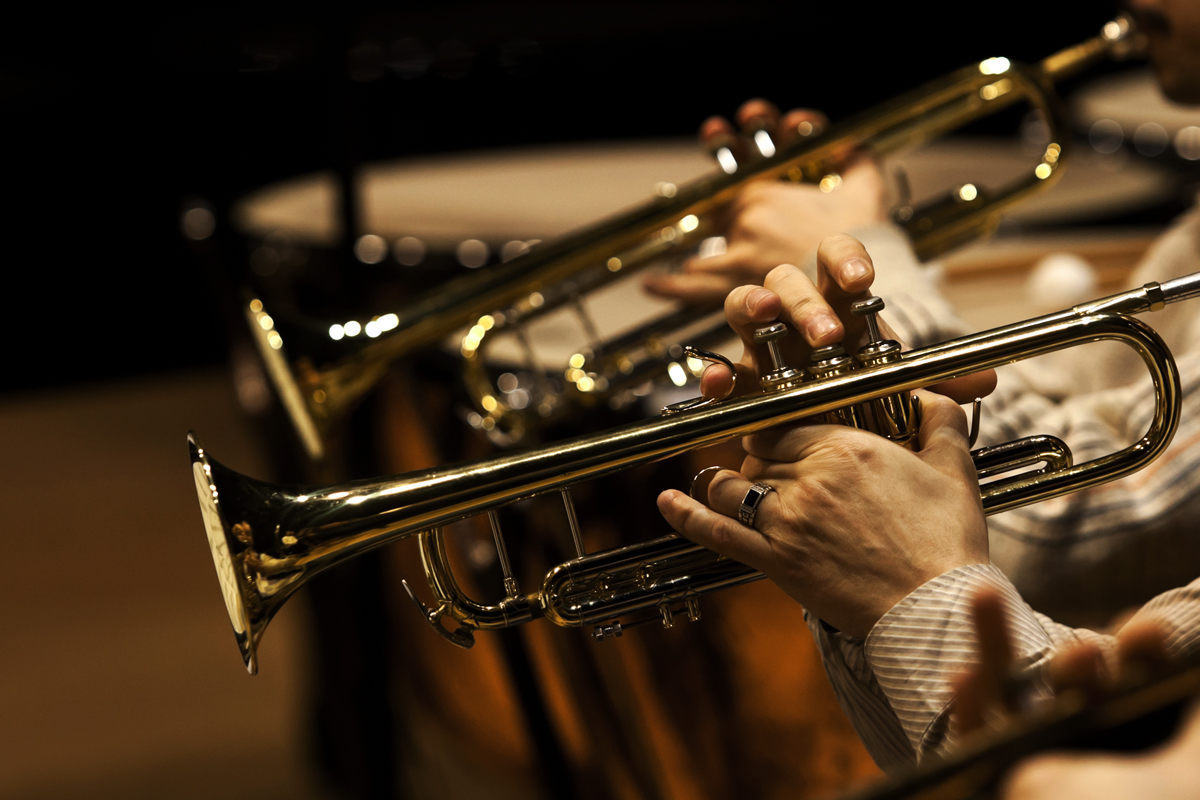
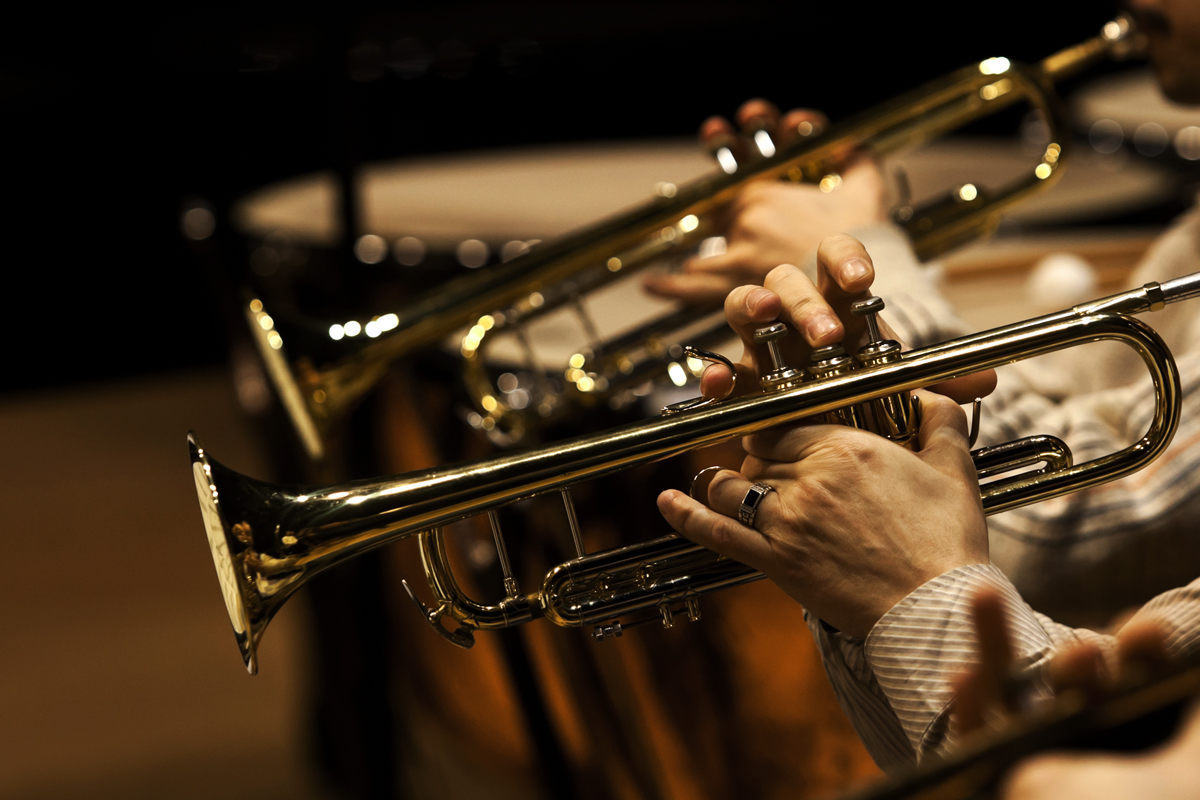
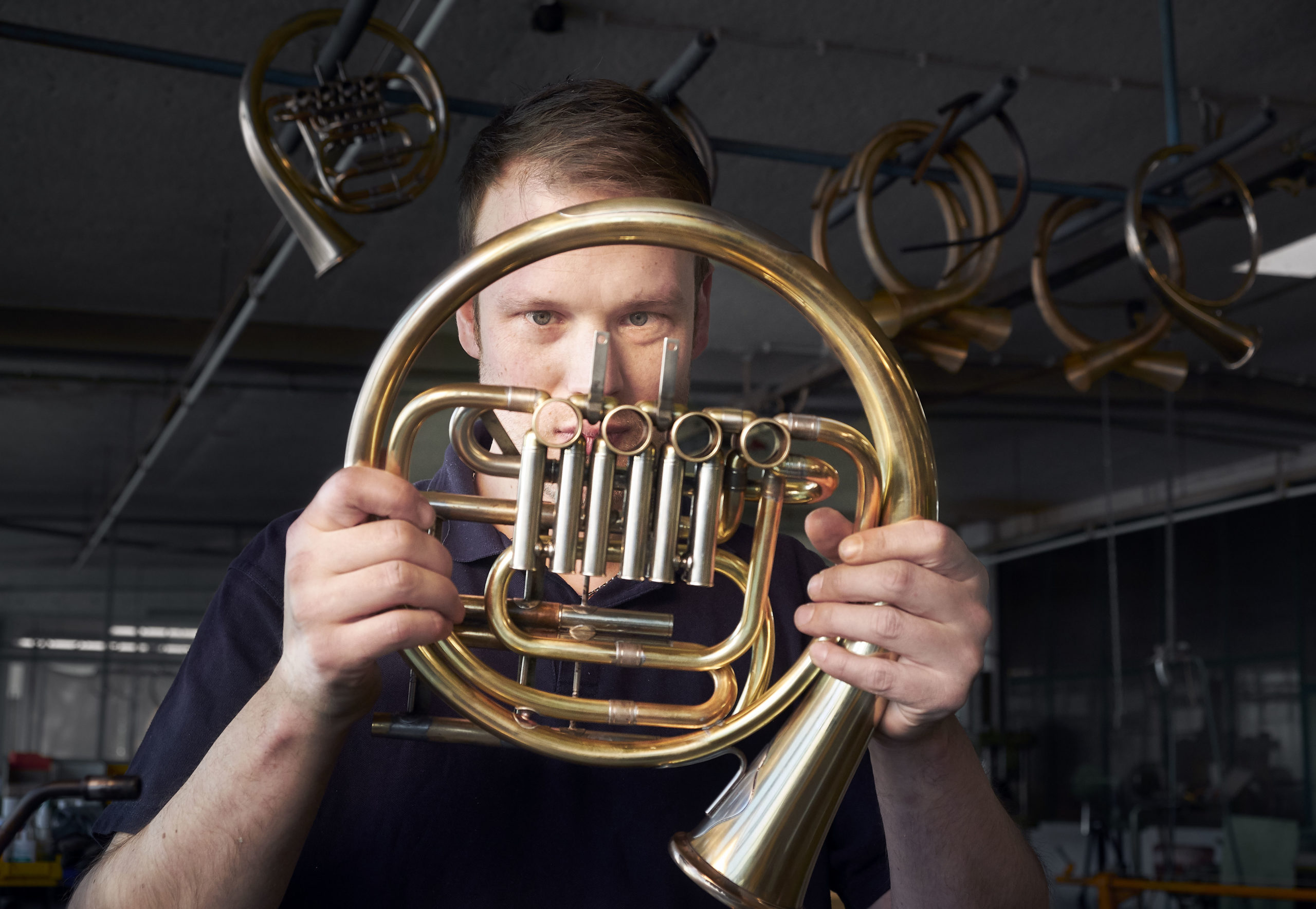
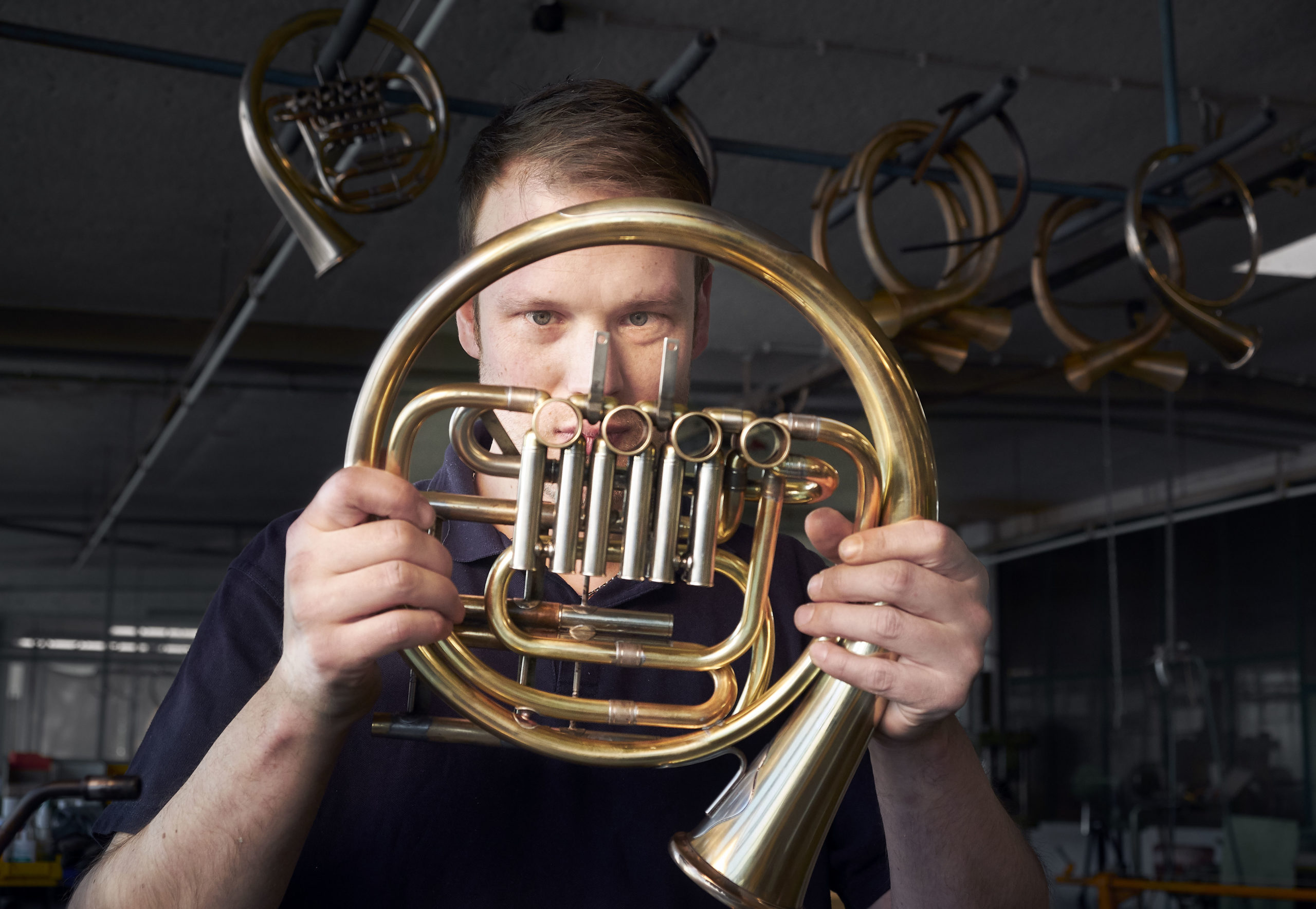
Patented instrument technology
FINKE has a number of patent applications for horn construction. Of course, these patents also improved the other brass instruments.